The CANDU-600
Preamble
The large majority of nuclear reactors are designed and operated to achieve a self-sustained neutron chain reaction in some combination of fissile, fissionable, fertile and other materials. In a nuclear power plant,the nuclear reactor transfers the energy released from the fission process to a thermal loop whose main functions is the powering of a turbine for the production of electricity.
A word about Energy
Energy is often defined as the ability to do work. Energy is a conserved and quantitative property that is transferred to a body or to a physical system, recognizable in the performance of work and in the form of heat and light. The first law of thermodynamics expresses this idea: the law of conservation of energy states that energy can be converted in form, but not created or destroyed.
Nuclear Engineering begins with the idea that matter and energy may also be converted to one another. This simple fact was articulated by Einstein in his famous formula: E=mc2.
Nuclear binding energy is the minimum energy that is required to disassemble the nucleus of an atom into its constituent protons and neutrons, known collectively as nucleons. The binding energy for stable nuclei is always a positive number, as the nucleus must gain energy for the nucleons to move apart from each other. Nucleons are attracted to each other by the strong nuclear force. The mass of an atomic nucleus is less than the sum of the individual masses of the free constituent protons and neutrons. The difference in mass can be calculated by the Einstein equation, E = mc2, where E is the nuclear binding energy, c is the speed of light, and m is the difference in mass. This 'missing mass' is known as the mass defect, and represents the energy released when the nucleus was formed.
The unit of measurement for energy in the International System of Units (SI) is the joule (J).
A word about History
The nuclear industry in the United States, and Canada, grew out of the Manhattan Project, which was the large science and engineering effort during WWII that led to the development and use of the atomic bomb. Even today, the heritage continues to cast a shadow over the nuclear industry. The goal of the Manhattan Project was the production of very highly enriched uranium and very pure plutonium-239 contaminated with a minimum of other plutonium isotopes. These were the materials used in the production of atomic weapons. Today, excess quantities of these materials are being diluted so that they can be used in nuclear-powered electric generating plants.
The nuclear industry today is truly international in scope. Major design and manufacturing companies work all over the world. The industry in the U.S. has survived the 30 years since the Three Mile Island accident, and is resurging to meet the coming requirements for the generation of electric energy. The companies may have new ownership and new names, but some of the people who began their careers in the 1970s are still hard at work and are involved in training the coming generations of workers.
It is important to recognize that when the commercial nuclear industry began, we did not have high-speed digital computers or electronic hand calculators. The engineers worked with vast tables of data and their slide-rules; draftsmen worked at a drawing board with a pencil and ruler. The data were compiled in handbooks and manually researched. Today, that information is available on the Internet and in the sophisticated computer programs that are used in the design and engineering process.
This document is devoted to a particular nuclear power reactor system: The CANDU-600(Canadian Deuterium Uranium Reactor-600).
Among the reactor technologies with operational history the CANDU-600 is unique in that it uses heavy water (sometimes called deuterium oxide) as its neutron moderator. Because it uses heavy water as a moderator, the reactor can use natural uranium as a fuel; therefore, the front-end of the fuel cycle does not include the uranium enrichment process required for reactors with a light water neutron moderator.
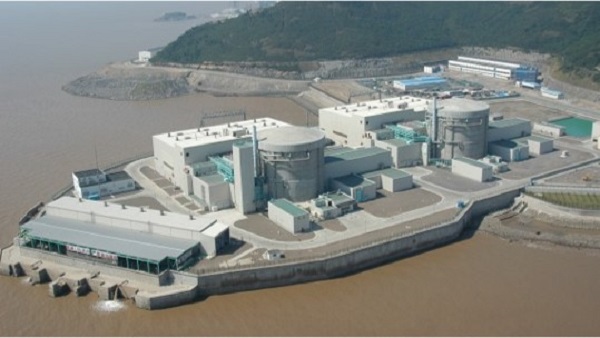
Introduction to CANDU Technologies
The Senior Engineer of AscenTrust has been involved with the Canadian Deuterium Reactor technologies since 1969. It is therefore natural that we would be involved in the licensing of the CANDU, in the U.S.
The CANDU can only be licensed in the US through the new regulatory environment referred to as 10 CFR Part 53 . As far as licensing is concerned the CANDU has two major technical problems. The first problem is the lack of a pressure vessel and the second is the positive coeficient of reactivity.
The CANDU Owners Group (COG) are proceeding with the development and deployment of advanced technologies and small modular reactors (SMRs) in Canada and worldwide.
CANDU stands for CANada Deuterium Uranium. A CANDU is a type of nuclear reactor with technology to use non enriched fuel developed by Canada. Currently, seven countries in this world have CANDU type reactors: Canada, India, China, Pakistan, South Korea, Argentina and Romania.
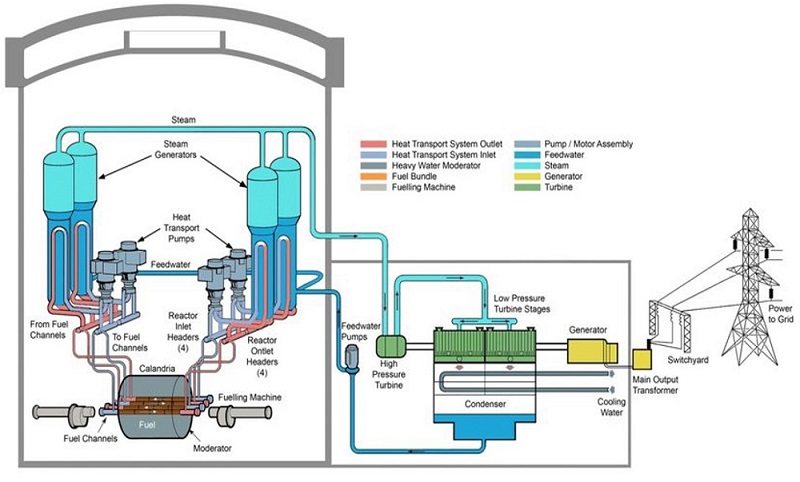
Why use heavy water?
The neutron which is emitted from a nuclear fission reaction is an ~MeV neutron. However, due to the fact that the absorption cross section for Uranium of a thermal(0.025eV) neutron is orders of magnitude higher than MeV neutrons, one needs to thermalize these neutrons. At the same time, we do not want the thermalizeing agent to absorb the neutrons. It is also desirable that a neutron loses a lot of energy in each collision. These factors, are accounted in the number called the Moderating Ratio which is proportional to scattering cross section for neutrons, energy lost in each collision, and inversly proportional to absorption cross section. This number works out to be 58 for light water and 21000 for heavy water. It is this large value of the moderating ratio that allows CANDU reactors to use Natural Uranium without enrichment.
The heavy water coolant flows in pressure tubes horizontally as it provides higher symmetry. However, there is a large mass of the pressure tube inside the reactor and it can potentially absorb too many neutrons to sabotage reactor criticality. The solution to this problem came via Zirconium which happens to have a very low neutron absorption cross section. It is worth mentioning that this result came as a product of materials research in Chalk River for the US nuclear program.
Although, in principle, the coolent can be anything, all operating CANDU reactors have heavy water as coolent as the use of heavy water maximises neutron economy.
The CANDU-600
The CANDU-600 nuclear power stations has consistently proven to be competitive with other types of nuclear power plants, while offering unique advantages to their operators. Some of the design features and unique characteristics of the CANDU-600 reactor are:
• a reactor core comprising several hundred small diameter fuel channels rather than one huge pressure vessel
• heavy water (D2O) for moderator and coolant
• separate high pressure fuel moderating and cooling systems contained in horizontal channels
• fuel channels are contained in a stainless vessel (calandria) filled with heavy water as an additional moderating medium
• on-power refuelling
• reactivity devices that are located in the cool low pressure moderator, and not subjected to high temperatures or pressures
• natural uranium fuel or other low fissile content fuel
• reduced consequences from accidental reactivity fluctuations — excess reactivity available from the fuel is small and the relatively long lifetime of prompt neutrons in the reactor precludes rapid changes in power levels
• two fully capable safety shutdown systems, independent from each other and the reactor regulating system.
The following Technical Summary provides an overview of the CANDU 6 nuclear power system. All CANDU 6 power plants are fundamentally the same, although there are differences in detail: these largely result from different site conditions, and from improvements made in the newer designs.
Section One: Introduction
The CANDU-600 is a proven and mature design to help countries reach their goal of Net Zero. Built on proven CANDU technology to be quickly deployable, this 600 MW(e) reactor features simplified systems, fewer components and a modular design. The design objectives are a low-cost, low-carbon power with a high capacity factor in a compact layout.
Section Two: Target Application
The CANDU-600 is designed to enable deployment using only proven technology, maintaining energy independence by using natural uranium fuel from fuel manufacturers and avoiding the need to import enriched uranium fuel. This maximizes identification and utilization of a high performing supply chain, minimizing project delivery risk and creating high technology jobs in countries. The CANDU-600 is a proven reactor technology with a design life of 70 years (extendable to 100 years) and a 90% capacity factor. It can accommodate to a broad range of potential reactor sites, with its 0.3g seismic design, compact shape and grid-stability features.
Section Three: Main Design Features
1.   Design Philosophy: The CANDU-600 is based on a decades-long proven design that is licensed in many countries operating CANDU reactors. It meets modern regulatory requirements, with dedicated post-Fukushima features. The CANDU-600 does not require enriched fuel or a fuel-qualification program because it relies on natural Uranium in the same fuel bundle employed in multiple CANDU6 reactors. To achieve this it uses heavy water for moderation and cooling.
2.   Nuclear Steam Supply System: Nuclear Steam Supply System
A CANDU 6 nuclear steam supply system’s power production process starts like that of any other nuclear steam supply system, with controlled fission in the reactor core. However, unlike other reactors, the CANDU 6 is fuelled with natural uranium fuel that is distributed among 380 fuel channels. Each six-meter-long fuel channel contains 12 fuel bundles. The fuel channels are housed in a horizontal cylindrical tank (called a calandria) that contains cool heavy water (D 2 O) moderator at low pressure. Fuelling machines connect to each fuel channel as necessary to provide on-power refuelling; this eliminates the need for refuelling outages. The CSMR is a horizontal pressure tube, pressurized heavy water reactor developed from the long lineage of successful CANDU reactors. The reactor core consists of a horizontal calandria housing a set of pressure tubes. The reactor coolant system consists of these pressure tubes, two steam generators, four primary circulation pumps plus interconnecting piping and headers. The calandria itself is filled with heavy water that surrounds the pressure tubes and provides neutron moderation plus an element of safety, with the calandria operating as a core catcher for severe accidents.
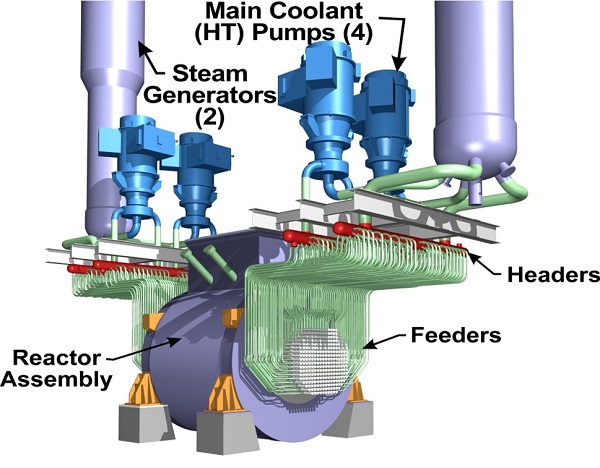
3.   Reactor Core:
The CSMR core is 176 channels in a lattice of 14 rows and 14 columns. The channel array is 12’ 2” across. The calandria main shell radius is 285 cm. Reactor is fueled by standard CANDU natural uranium fuel bundle.
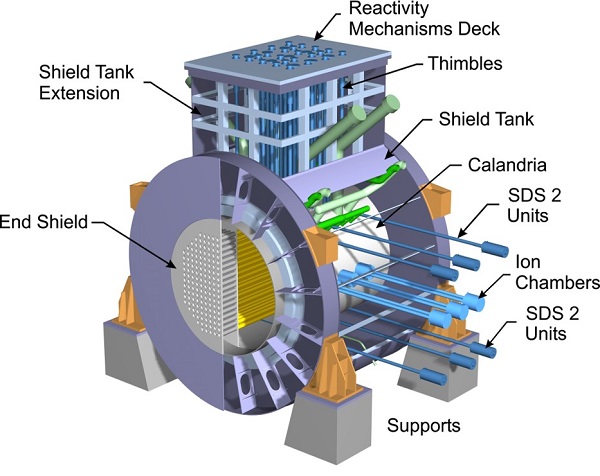
4.   Reactivity Control: Reactor control uses eight zone control units to provide the primary means of reactivity regulation during normal operation. The core design allows control to be achieved through very small changes in these zone control units. The adjuster rods, absorber rods and ability to use soluble poisons found in traditional CANDU designs are retained, as are two fully independent, diverse safety-shutdown systems: SDS1 and SDS2. Like its predecessors, the CSMR provides safety shutdown reliability.
5.   Reactor Pressure Vessel and Internals: The reactor consists of a cylindrical calandria and end shield assembly that is enclosed and supported by the cylindrical shield tank and its end walls. The cylindrical shield tank extension 1assembly closes the top of both vessels. The calandria contains the heavy water moderator and reflector; the shield tank contains light water. The seismically-qualified moderator system is independent from the pressurized heavy water heat transport system (HTS) in the fuel channel assemblies and has the inlet and outlet nozzles connected high in the calandria to enhance performance in the event of a severe accident.
6.   Reactor Coolant System: The HTS is a single figure-of-eight loop with two steam generators and four heat transport pumps. The HTS is seismically qualified such that a seismic-induced LOCA is outside of the design basis.
7.   Steam Generator: Two steam generators are used, both with inverted U-tubes and integral steam drum and preheaters, and located inside the containment structure.
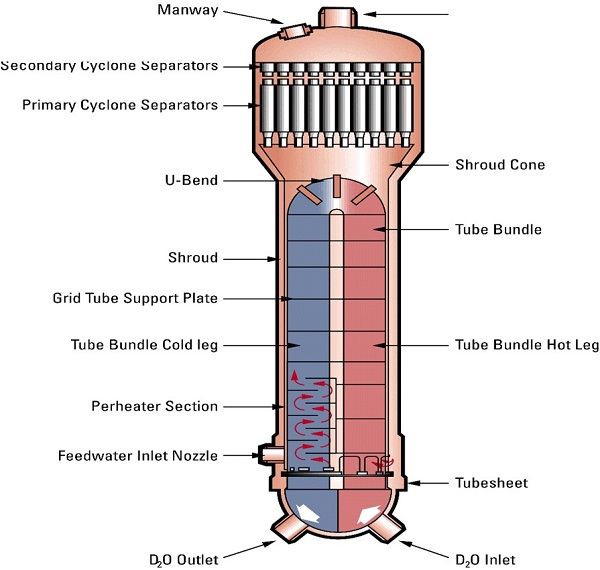
8.   Pressurizer: he pressure and inventory control system include a pressurizer, bleed condenser, feed pumps (one operating; one on standby), a storage tank and control valves.
Section Four: Safety Features
The CSMR safety features establish defence-in-depth against radiological hazards. CSMR leverages the inherent safety characteristics of the basic CANDU reactor design and supplements them with a judicious application of passive and active safety features that emphasizes provenness and results in an improvement in safety. The irradiated fuel bay is a robust, seismically qualified structure with a large volume of water relative to the decay heat load of discharged fuel, providing many days of passive cooling in the event of a loss of active heat removal.
The CSMR provides large volumes of water that are available to provide cooling to the core in the event of accidents, including by passive means. In addition, it has a large containment volume, contributing to minimizing hydrogen concentrations in severe accidents. The CSMR HTS is seismically qualified to the design basis earthquake. The CSMR also makes use of loop subdivision and feeder interlacing to reduce the rate of coolant voiding that is possible in the event of a large HTS pipe break.
The CSMR places all reactivity devices in the separate, low-temperature, low-pressure moderator, eliminating pressure-driven ejection of reactivity devices from the design. The separation of moderator from coolant also provides two separate heat removal means in the event of accidents and ensures that moderator temperature feedback to the core physics is negligible in normal operation. The characteristic CANDU pressure-tube design means that direct containment heating type of severe accident does not occur in this design.
1.   Engineered Safety System Approach and Configuration : All plant systems are assigned to one of two groups (group 1 or group 2) according to the CSMR grouping and separation approach. Group 1 includes the power production systems and delivers safety functions for group 2 support. Group 2 includes the safety related systems required for mitigation of accidents and group 2 systems are qualified or protected to provide safety functions in the event of severe external events. There is additional separation within the groups.
The CSMR has two separate shutdown systems. These are two fully-capable fast-acting means of shutdown for use at the third level of defence in depth, fully independent of each other and of the reactor regulating system which acts at the second level of defence in depth.
2.   Decay Heat Removal System
Decay heat removal is accomplished in CSMR by application of several provisions in the design, including three group 2 systems, as follows:
The large inventory in the HTS, including the pressurizer inventory, provides heat removal for normal operating transients. The HTS layout enhances natural circulation to the steam generators, which have a large inventory. The steam generators have normal make-up capability and back-up feedwater.
When the steam generators are not available, or are not effective for heat removal, heat can be removed from the HTS using the shutdown cooling system. Under emergency conditions this system can be valved in at full HTS pressure and temperature.
3.   Emergency Core Cooling System
The emergency core cooling system supplies emergency coolant to the reactor headers in the event of a loss- of-coolant accident (LOCA). The system operation is divided into two parts, short-term injection and long- term recirculation. Short-term injection consists of two stages: high pressure and low pressure injection. During the high pressure injection stage, water from the accumulator tanks is injected into the HTS by pressurized gas. After this water is depleted, low pressure injection automatically takes over, injecting water from a grade level tank via the emergency core cooling pumps. A connection is provided to this tank for demineralized water makeup, and for initial filling. For small LOCAs provision of steam generator crash cooldown and the maintenance of continued feedwater flow is used instead of the ECC heat exchangers to provide cooling. The crash cooldown is performed via the MSSVs.
4.   Containment System
The basic function of the containment system is to form a continuous, pressure-confining envelope about the reactor core and primary cooling system in order to limit the release of radioactive material to the external environment resulting from an accident. This accident could be either a failure of fuel cooling, or an accident which releases radioactive material into the containment without a rise in containment internal pressure.
To achieve this overall function, the containment system includes the following related safety functions:
i.   Isolation: to ensure closure of all openings in containment when an accident occurs.
ii.   Pressure/activity reduction: to control and assist in reducing the internal pressure and free radioactive material released into containment by an accident.
iii.   Hydrogen control: to limit concentrations of hydrogen/deuterium within containment after an accident to prevent detonation.
iv.   Monitoring: to monitor conditions within containment and the status of containment equipment, before, during and after an accident.
In addition to its safety role, the containment structure also serves the following functions:
i.   To limit the release of radioactive materials from the reactor to the environment during normal operations.
ii.   To provide external shielding against radiation sources within containment during normal operations and after an accident.
iii.   To protect reactor systems against external events such as tornados, floods, etc.
The containment system includes a reinforced concrete containment structure (the reactor building)with a reinforced concrete dome and an internal steel liner, access airlocks, equipment hatch, building air coolers for pressure reduction, and a containment isolation system.
5.   Plant Safety and Operational Performances
The CSMR design aligns with the concept of defence in depth, leveraging inherent safety features through the application of proven engineered systems with an emphasis on providing high reliability through a prudent mix of active and passive features. The overall CSMR design philosophy is to reduce total unit energy cost by reducing specific capital cost, shortening the construction schedule, reducing operating, maintenance and administration costs and providing for plant life extension. In addition, CSMR enhances or improves the traditional CANDU advantages including real safety, low man-rem exposure, high capacity factor and ease of maintenance. Proven systems, system parameters, components, and concepts are used, including proven technologies from other industries.
6.   Instrumentation and Control Systems
The overall I&C architecture and design is aligned with the five levels of defense-in-depth, with suitable independence between the different levels. Most automated plant control functions are implemented in a modern distributed control system (DCS) using a network of modular, programmable controllers that communicate with one another using reliable, high-security data transmission methods. The plant is automated to the extent that requires a minimum of operator actions for all phases of operation.
The control systems are backed up by the safety systems, which include the two independent shutdown systems, the emergency core cooling system, emergency heat removal system, and the containment system. Each of these safety systems operates completely independent of the other and independent of the reactor and process control systems.
7.   Plant Layout Arrangement
The CSMR layout is arranged to minimize and achieve a short practical construction schedule. This is achieved by simplifying the layout, optimizing interfaces, reducing construction congestion, providing access to all areas, providing flexible equipment installation sequences and reducing material handling requirements. The principal structures of the CSMR include the reactor building, the reactor auxiliary building, the turbine building, the group 1 service building and maintenance building. The auxiliary structures include the Group 1 pump house (main pump house), Group 2 pump house and administration building. In general, Group 1 systems sustain normal plant operation and power production, while Group 2 systems have a safety or safety support functions.
Candu Energy Inc. has requested the CNSC to initiate the formal Vendor Design Review (VDR) process for the CSMR design, which will be conducted based on the regulatory requirements applicable to the new build projects in Canada. The design of CSMR is at the Conceptual Design stage. The current scope is to confirm the safety and OPEX driven design changes affecting NSP in support of licensing review, and to finalize the testing schedule to support Preliminary Safety Analysis Report (PSAR) development and detailed design.
1.   Fuel Cycle Approach: The standard CSMR uses a once-through fuel cycle based on natural uranium, producing a very low residual- uranium spent fuel with low heat generation. It is also capable of burning recovered uranium from light-water reactors, making it a valuable addition to any light-water fleet. The use of MOX and Thorium fuels are also possible with suitable customization.
2.   Waste Management and Disposal Plan: The CSMR implements systems and equipment for handling radioactive wastes consistent with the state-of- the-art in Canada. The radioactive waste management systems are designed with the objective of limiting routine releases in accord with the ALARA principle. Facilities are provided for interim storage, or controlled release, of all radioactive gaseous, liquid and solid wastes. It is anticipated that most of the of low-level and intermediate-level solid waste produced over the reactor’s 70-plus year lifetime will be stored at the waste management area, with high-level waste being stored on-site in a dry storage facility. Candu Energy Inc. is working on establishing the plan to safely store, handle and dispose of all the spent fuel including the on-site storage, long term storage and potential design for new long- term storage containers that meet the requirements for the deep geological repository design of the Nuclear Waste Management Organization (NWMO).